"ההדפסה בתלת-מימד תאפשר ייצור של שבבים תלת-מימדיים"
כך אמר עמית דרור, מנכ"ל ננו דיימנשן ● לדבריו, "לפני כמה עשרות שנים, אלקטרוניקה היתה תלת-מימדית, אך היום זה נראה אחרת - יש לנו סמארטפונים ואינסוף מכשירים המבוססים על מעגלים אלקטרונים מודפסים"

"ההדפסה בתלת-מימד תאפשר ייצור של שבבים תלת-מימדיים. השינוי איננו רק בשלב הייצור אלא כבר בשלב הפיתוח", כך אמר עמית דרור, מנכ"ל ננו דיימנשן.
דרור דיבר בכנס 3D Printing Israel 2016 בהפקת אנשים ומחשבים, אשר התקיים היום במרכז הכנסים LAGO בראשון לציון. את הכנס הנחה יריב ענבר, מנכ"ל מדיאטק-ג'ון ברייס היי-טק.
לדבריו, "התהליך שבו אנו רואים פתרונות יישומיים נכנסים לתעשיה, רלוונטי גם לעולם האלקטרוניקה. לפני כמה עשרות שנים אלקטרוניקה היתה תלת-מימדית. היום זה נראה אחרת. יש לנו סמארטפונים ואינסוף מכשירים המבוססים על מעגלים אלקטרונים מודפסים. עדיין, הם לא לגמרי שטוחים. יש הרבה רכיבים עם רגליים קטנות שמתלבשים על המעגל המודפס".
"ננו דיימנשן מסתכלת קדימה לקראת עידן ההדפסה התלת-מימדית של מעגלים אלקטרוניים. אלקטרוניקה נוגעת לכל דבר בחיינו – תעשיית הרכב, טלקום, מוצרי צריכה ואינטרנט של הדברים, ומיכשור רפואי".
לשלב את הרכיבים בצורה מדויקת יותר
לדברי דרור, "היום מדברים על אלקטרוניקה מודפסת – בסיס ועליו מדפיסים ליתוגרפיה של המעגלים, האנטנות מסכי המגע ועוד. ההדפסה הזו מאפשרת לשלב את הרכיבים בצורה מדויקת יותר וגמישה ביחס לעבודה עם התהליכים הקלאסיים".
"המעגל המודפס הקלאסי הוא תלת-מימדי, אבל התהליך שבו מייצרים אותו איננו בתהליך של Additive Manufacturing. מייצרים מספר שכבות שיש עליהם מוליכים ושכבות מבודדות, מצמידים אותן זו לזו, לאחר מכן מבצעים קידוחים ומחברים בין השכבות".
"כשאנחנו מדברים על אלקטרוניקה תלת-מימדית מודפסת – בתהליך אדיטיבי – אנחנו מדפיסים את השכבות האלה על כל החומרים הרלוונטיים שהם בעצם חומר מוליך, חומר מבודד, שכשנייצר את שכבת המוליכים הבאה לא נייצר קצר".
"היום המהנדסים יושבים מול מחשב ומבצעים תכנון של דגם האלקטרוניקה הבא", אמר דרור. "הם עובדים על תוכנה ועלינו לקחת את אותו קובץ תכנון, להמיר אותו לקובץ שמכיל נתונים על מספר שכבות של אלקטרוניקה לתלת-מימד, ואז על המדפסת לקחת את החומרים ולהדפיס כרטיס אלקטרוני רב שכבתי".
שולטים על החומרים עצמם
לדבריו, "הרעיון הוא לאפשר למהנדסי אלקטרוניקה לקחת את התכנונים שלהם, ובמקום להעביר לצד ג' ולהמתין ימים או שבועות כדי לקבל את המעגל מוכן, הם יוכלו לפנות למדפסת ולייצר את האינטראקציה המהירה בתוך המפעל שלהם. הדפסת כרטיס בעל 10 שכבות תיארך בסדר גודל של 10 שעות".
בגלל היכולת שלנו לשלוט על החומר, אמר דרור, "אפשר ליצור כרטיס גמיש וגם קשיח. אלה יתרונות שיש כששולטים על החומרים עצמם – דבר שלא אפשרי בתהליכים קלאסיים שבהם לוקחים מצע מן המוכן. היום אנחנו עונים על כל הסטנדרטים של התעשיה. המגבלה שלנו לא נובעת מכמות השכבות אצלנו. הסוגיה הזו לא קיימת, כי ההדפסה היא פונקציה של ציר ה-Z של המדפסת. אם שכבה היא 50 מיקרון – בשניים-שלושה מילימטר אפשר להכניס עשרות שכבות.
אחד הדברים המעניינים הוא לתת מענה מעבר ל-PCB – צורות תלת-מימדיות שאפשר להדפיס על המוצרים, או הדפסה של מוצר שלם. אם משלבים גם את הדפסת הפולימרים, זה מאפשר לתעשיה שיטות ייצור חדשות, ולמתכננים שיטות תכנון חדשות שאינן מוגבלות בגלל שיטות הייצור. זה העתיד ואני מאמין שבשנים הקרובות נראה יותר ויותר פתרונות יישומיים. למכשירים לבישים, האינטרנט של הדברים. ועוד.
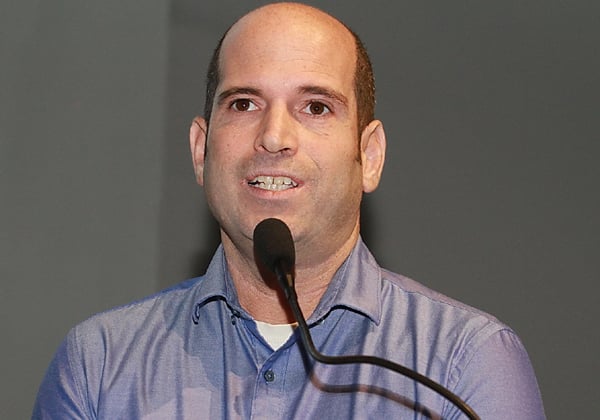
זיו שדה, מנכ"ל סו-פאד. צילום: ניב קנטור
לדברי זיו שדה, מנכ"ל סו-פאד – נציגת סטרטאסיס (Stratasys) בישראל, תיאר דוגמה לשימוש במדפסת J750 של סטרטאסיס, בניתוח שנערך בבית החולים איכילוב. "מדובר בגידול שהיה קרוב מאוד למפרק הברך. למנתחים היה קשה להסיר את הגידול ביד חופשית, משום שחלקו נמצא גם בתוך העצם, מבלי לגרום נזק גדול למטופל".
"המערכת קיבלה את קבצי ההדמיה של האיזור המנותח והפכה אותם מהדמיה דו-מימדית לקובץ תלת-מימדי, ולאחר מכן מדפיסים את המודל האנטומי של האיזור כדי שהמנתחים יוכלו לתכנן טוב יותר את הניתוח. כמו כן הם גם הדפיסו סד מיוחד המחליף את רקמת העצם עד להחלמתה".
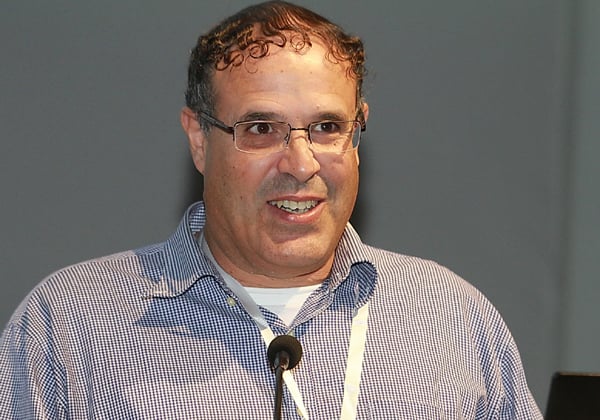
ד"ר עוז גולן, יו"ר ענף הנדסת חומרים בלשכת המהנדסים. צילום: ניב קנטור
ד"ר עוז גולן, יו"ר ענף הנדסת חומרים בלשכת המהנדסים, דיבר על היבטים מטלורגיים והנדסיים בהדפסה תלת-מימדית של טיטניום לתחום התעופה. לדבריו, "בהדפסה תלת-מימדית אין איבוד חומר כמו בעיבוד שבבי, ויש חסכון עצום במחיר. אין צורך באחזקת מלאי. כבר כיום, אם במטוס F15 יש תקלה, שולחים בקשה לאמריקה שם מדפיסים את הרכיב בתלת-מימד ולמחרת הוא מוכן".
לדבריו, "להדפסה תלת-מימדית של רכיבי מטוסים זו יש כמה מגבלות: גודל הרכיב – מרבית המדפסות הן בעלות תא הדפסה קטן; טיב פני שטח ירוד; וכן, מדובר בטכנולוגיה חדשה שאין עליה נתונים הסטוריים – דבר החשוב בתעופה כדי שנוכל לחזות כיצד יתנהג החומר בעוד חמש ועשר שנים. לא ניתן לחזות זאת על סמך ניסוי קצר במעבדה של קורוזיה. בשל הדברים הללו, קצב אימוץ ההדפסה בתלת-מימד בתעופה עדיין איטי יחסית אבל זהו הכיוון".
תגובות
(0)